How to deal with the leakage of butterfly valve?
Posted by Bundor valve
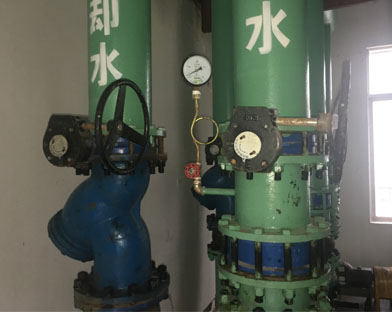
How to deal with the leakage of butterfly valve. Bundor Valve reminds you that there are many reasons for butterfly valve leakage, if you encounter this situation, you can take photos and send us after-sales solutions.In addition, this article will introduce you to two common possibilities of butterfly valve leakage, and introduce the treatment methods for you.
There are generally two possibilities:1. Seat leakage, the reason may be improper selection of seat material, or valve manufacturing problems, inappropriate installation caused by the solution to replace the seat.
- Stem leakage, which is a common problem, is usually due to improper installation of O-rings or bottom bushings, which can be solved by replacing O-rings or bushings.
Leakage of butterfly valves is divided into internal leakage and external leakage. The leakage of the stuffing box is usually called external leakage. The leakage of the closing part is called internal leakage, and the leakage of the closing part is not easy to find in the valve.Let's go into details.
Leakage of closure parts (internal leakage) can be divided into two categories.One is leakage of sealing surface.The other is leakage at the root of the seal.The causes of leakage are as follows:
- The sealing surface is not grinded well.
- The seal ring is not tightly matched with the seat and the valve handle.
- The connection between the valve handle and the stem is not reliable.
- Stem bending and torsion, so that the upper and lower closures are not in alignment;
- Close too fast, the sealing surface is not in good contact or has been damaged.
- The material selection is inappropriate and can not withstand the corrosion of the medium.
- The sealing surface can not withstand the impact of high-speed flowing media by adjusting the globe valve and gate valve.
- Certain media will gradually cool down after the valve closes, resulting in slits on the sealing surface and erosion.
- Threaded connections between some sealing rings, seats and valve runs can easily lead to oxygen concentration batteries and corrosion loosening.
- The valve can not be closed strictly because of the embedding of impurities such as welding slag, rust and dust, or the falling off and blocking of the valve core by another mechanical part in the production system.
- Open-air valves lack protection. Stem threads are covered with dust or corroded by rain, dew, frost and snow.
Leakage of stuffing box is often seen in factories.The reasons for the leakage of packing box are as follows:
- The corrosiveness, temperature and pressure of filler and working medium are not compatible.
- The incorrect filling method, especially the whole packing backup screw-in, is most likely to cause leakage.
- Insufficient machining accuracy or surface finish of the valve stem, ellipticity or notch;
- The stem has been pitted or rusted due to lack of protection in the open air.
- Stem bending;
- The filler has been aging for too long.
7. Operation is too fierce.