Description and classification of valve connection modes
Posted by Bundor valve
Description and classification of valve connection modes:
Nowadays, the application scope of valves is more and more extensive, and corresponding valves should be used in different environments.The connection between valve and pipeline or equipment is different.Attention shall be paid to the installation, use and maintenance of valves. Improper valve connection mode may lead to valve leakage, bleeding, dripping, etc.Therefore, the valve user should select the valve according to the actual conditions.
There are many types of valve connection, and the common valve connection methods are:Flange connection, wafer connection, butt welding connection, threaded connection, ferrule connection, clamp connection, self sealing connection, etc.
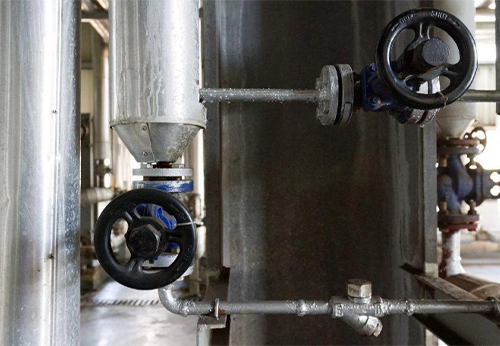
Threaded valve
A simple connection method, commonly used for small valves.This connection usually processes the inlet and outlet ends of the valve into taper pipe or straight pipe threads, which can be connected to taper pipe threaded joints or pipelines.Because this connection may have large leakage channels, so sealant, sealing tape or filler can be used to block these channels.If the material of the valve body can be welded, but the expansion coefficient varies greatly, or the operating temperature varies widely, the threaded connection must be sealed.Threaded valves are mainly those with nominal diameter less than 50mm.Path size, if too large, the junction is very difficult to install and seal.In order to facilitate the installation and removal of threaded connection valves, piping system at the appropriate location can be used on pipe joints.
Flanged valves
Flanged valves are the most commonly used connection type among valves.It is easy to install and remove.However, it is heavier than the threaded valve, and the corresponding price is also high.Therefore, it is suitable for pipe connection of various diameters and pressures.
Welding valve
This type of connection is applicable to various pressures and temperatures, and is more reliable than flange connection when used under relatively high load conditions.However, it is difficult to disassemble and reinstall the valves connected by welding,therefore, its use is limited to the occasions where it can normally operate reliably for a long time, or where the service conditions are high and the temperature is high.For example, it is used on the pipelines of thermal power plants, nuclear power projects and ethylene projects.As the socket welding forms a gap between the socket and the pipe, the gap may be corroded by some media,at the same time, the vibration of the pipe will make the connection part fatigue, so the use of socket welding is limited.When the nominal diameter is large, the service conditions are engraved, and the temperature is high, the valve body often adopts groove butt welding,at the same time, there are strict requirements for welding joints, and skilled welders must be selected to complete this work.
Nowadays, the application scope of valves is more and more extensive, and corresponding valves should be used in different environments.The connection between valve and pipeline or equipment is different.Attention shall be paid to the installation, use and maintenance of valves. Improper valve connection mode may lead to valve leakage, bleeding, dripping, etc.Therefore, the valve user should select the valve according to the actual conditions.
There are many types of valve connection, and the common valve connection methods are:Flange connection, wafer connection, butt welding connection, threaded connection, ferrule connection, clamp connection, self sealing connection, etc.
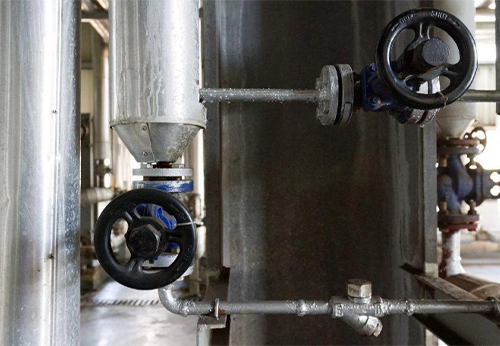
Threaded valve
A simple connection method, commonly used for small valves.This connection usually processes the inlet and outlet ends of the valve into taper pipe or straight pipe threads, which can be connected to taper pipe threaded joints or pipelines.Because this connection may have large leakage channels, so sealant, sealing tape or filler can be used to block these channels.If the material of the valve body can be welded, but the expansion coefficient varies greatly, or the operating temperature varies widely, the threaded connection must be sealed.Threaded valves are mainly those with nominal diameter less than 50mm.Path size, if too large, the junction is very difficult to install and seal.In order to facilitate the installation and removal of threaded connection valves, piping system at the appropriate location can be used on pipe joints.
Flanged valves
Flanged valves are the most commonly used connection type among valves.It is easy to install and remove.However, it is heavier than the threaded valve, and the corresponding price is also high.Therefore, it is suitable for pipe connection of various diameters and pressures.
Welding valve
This type of connection is applicable to various pressures and temperatures, and is more reliable than flange connection when used under relatively high load conditions.However, it is difficult to disassemble and reinstall the valves connected by welding,therefore, its use is limited to the occasions where it can normally operate reliably for a long time, or where the service conditions are high and the temperature is high.For example, it is used on the pipelines of thermal power plants, nuclear power projects and ethylene projects.As the socket welding forms a gap between the socket and the pipe, the gap may be corroded by some media,at the same time, the vibration of the pipe will make the connection part fatigue, so the use of socket welding is limited.When the nominal diameter is large, the service conditions are engraved, and the temperature is high, the valve body often adopts groove butt welding,at the same time, there are strict requirements for welding joints, and skilled welders must be selected to complete this work.